KTU Professor Collaborates with Airbus, Shell and Dallara Automobili: Carbon Fiber Composite Saves Lives

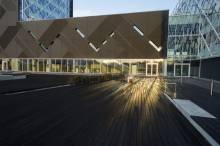
The quality of specialized constructions made of modern composite materials that can withstand extreme conditions - extremely high speed, obstacles in the race section - must be impeccable. A specialized carbon fiber composite body designed by the Italian company Dallara Automobili saved the life of a Haas driver in a recent Formula 1 race in Bahrain. KTU Prof. also contributes to the development and application of inspection methods for these structures. Researchers of K. Baršauskas Institute of Ultrasound Science.
Carbon fiber has two unique properties: lightness and strength. According to Kaunas University of Technology (KTU) Professor Renalds Raišutis, these features are very important in racing cars and aircraft.
“Carbon fiber withstands high static and dynamic loads, which is useful in extreme situations. It is for this reason that it is widely used to strengthen the structures of special purpose frames, beams and covering panels, ”says KTU Prof. R. Raišutis, Chief Researcher, K. Baršauskas Institute of Ultrasound.
In racing cars, carbon fiber replaces steel
Since 2015 Dallara Automobili is designing a specialized carbon fiber composite body for the Haas team. This company is world-famous for the body of the supercar Bugatti Chiron, which in 2019. the world speed record of that time was reached - 490 km / h. The body of this car was also made of carbon fiber composite.
The steel commonly used in the manufacture of racing car bodies is increasingly being replaced by carbon fiber, which is characterized by lightness and strength. The F-1 car has an open body - a capsule in which the racer sits. After the start in the race in Bahrain, Haas F1 driver Romain Grosjean entered the track fence at a speed of 225 km / h. The part of the capsule that protects the driver was detached from the impact.
According to R. Raišutis, this part of the capsule consists of a carbon fiber reinforced composite and covered with aramid fiber to protect the driver in the event of impacts of various strengths that occur when colliding with other cars or various obstacles on the race track.
“The blow was so strong that the six bolts connecting the driver’s protective capsule and the rear of the car to the engine and the rear suspension broke. It is important to mention that a special system of two-segment titanium arch and three supports is attached to this capsule that protects the driver's body in order to protect the rider's head in the event of a collision with various obstacles, ”says KTU Professor R. Raišutis.
Poor body quality can cost lives
The quality of specialized mechanical constructions - made of modern composite materials - must be impeccable, as such constructions must withstand extreme racing conditions.
“Structures must be inspected by appropriate non-destructive testing and condition monitoring methods to avoid dangerous internal defects. If they have internal defects, the structure may not withstand and break during operation or shocks, which may result in death, ”says the scientist.
Investigations of the internal structure of structures are performed by non-destructive testing methods: ultrasonic and X-ray.
"These complementary methods provide opportunities to" look "inside the object without mechanically destroying it. As a result, internal defects of glued composite structures, such as air bubbles, non-adhesions, delamination, are detected. Also internal cracks and weld seams of metal objects and internal defects of 3D printed plastic and metal objects, ”says R. Raišutis.
The professor notes that the time of the investigation depends on the type of object to be inspected and its dimensions, the complexity of the structure itself and the number of inspection sites that are critical to its integrity. Also from the properties of the material that makes up the structure or the set of materials used.
“KTU Prof. Researchers of K. Baršauskas Institute of Ultrasound Science ", says R. Raišutis.
In collaboration with industrial partners such as Airbus, Shell, Safran and Dallara Automobili, KTU Prof. K. Baršauskas Institute of Ultrasound is implementing a 4-year project. The aim of the project is to combine, for the first time, efficient methods of modeling and signal processing of ultrasonic wave propagation in various structures and to evaluate the reliability of the condition monitoring systems of these structures.
Posted By

GSP Admin